Discover how a leading lifestyle brand achieved significant top and bottom-line benefits through automated logistics processes that provide full visibility of inbound and outbound shipments.
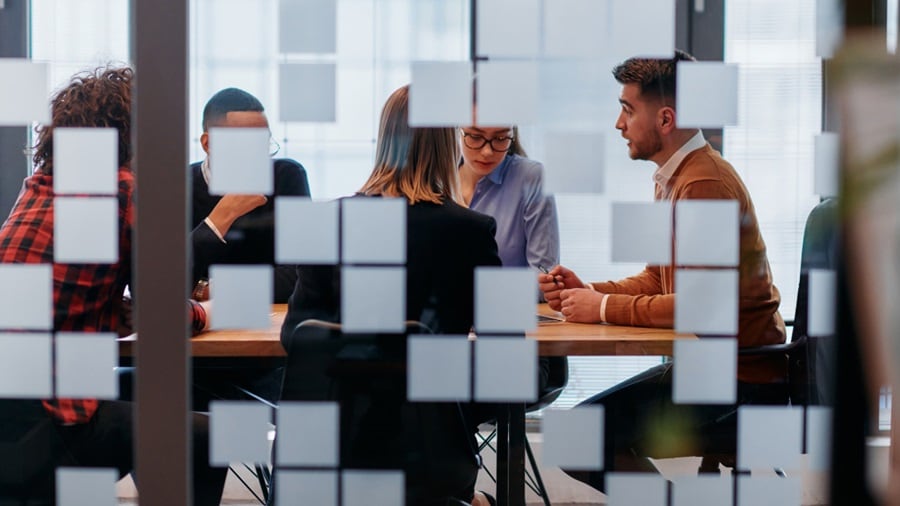
A strategic collaboration
A global apparel pioneer founded in 1853 - our customer is renowned for revolutionising denim. With Pakistan and Bangladesh serving as their primary sourcing markets, Maersk has played a critical role in optimising their regional logistics.
Our partnership began in 2011 with a modest 18,000 CBM. Over the years, it has evolved into a global engagement. Today, we manage 60–70% of their total logistics footprint. This includes integrated services across ocean freight, air, LCL, warehousing and distribution, Eco-Delivery, and end-to-end supply chain management.
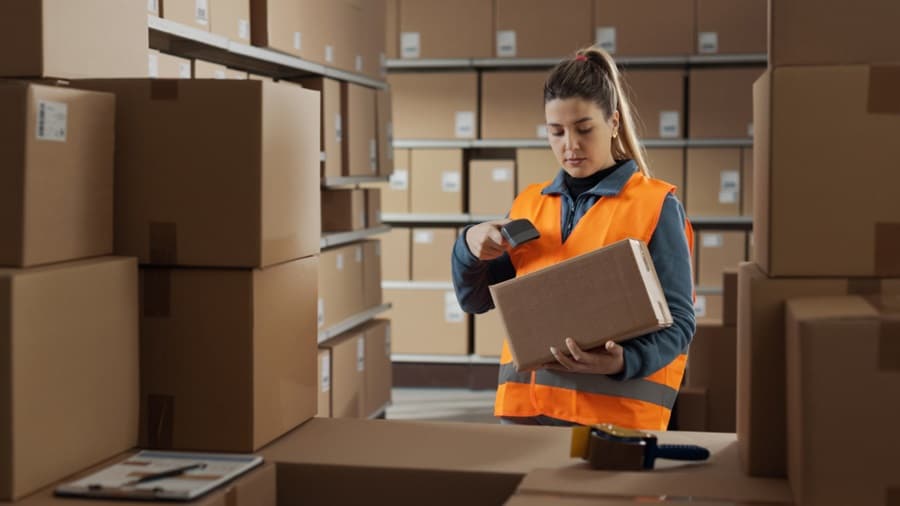
As a trusted 3PL partner, we manage their full logistics operations in Pakistan and around 30% in Bangladesh. As their ocean carrier, we handle 70–80% of volume from these sourcing hubs.
Addressing inventory challenges
Given our customer’s global presence and substantial cargo volume, issues such as pilferage and missing quantities at destinations were leading to carton and piece shortages, resulting in lost sales and revenue. Maintaining the right inventory levels in stores was crucial.
RFID solution implementation
To address these challenges, we proposed a RFID solution:
- Scanning: RFID scanning for each carton.
- Real-time validation: RFID EPC against UPC (Pre-ASN) through third-party software.
- Reporting: Manual discrepancy reporting through weekly reports.
Maersk RFID Cargo Flow
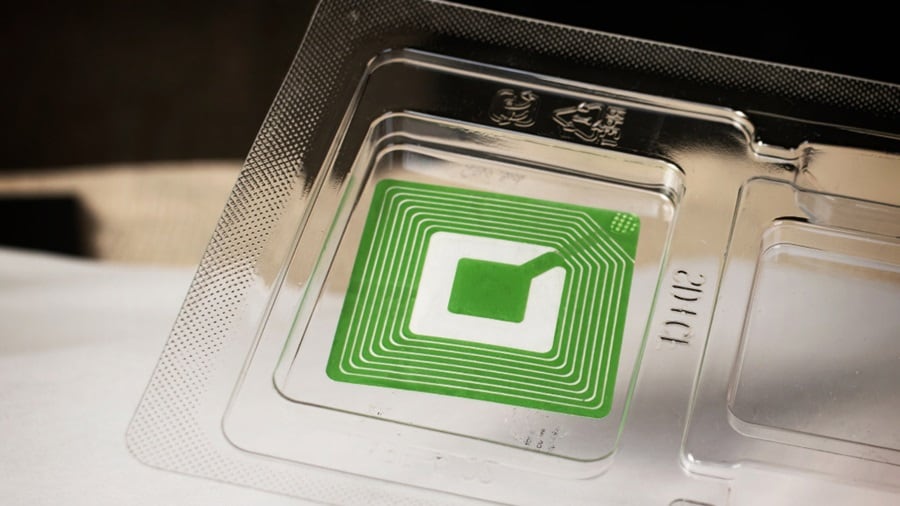
Benefits of RFID technology
Proven benefits of deploying RFID scanning technology at origin points, including:
- Enhanced inventory visibility
- Validation of factory packing accuracy
- Minimisation of cargo losses and pilferage
- Support for factory performance management and continuous improvement
- Early identification of issues and mitigation actions close to the factory
- Enabling item-level customised product operations at the origin, typically performed at the destination distribution centre
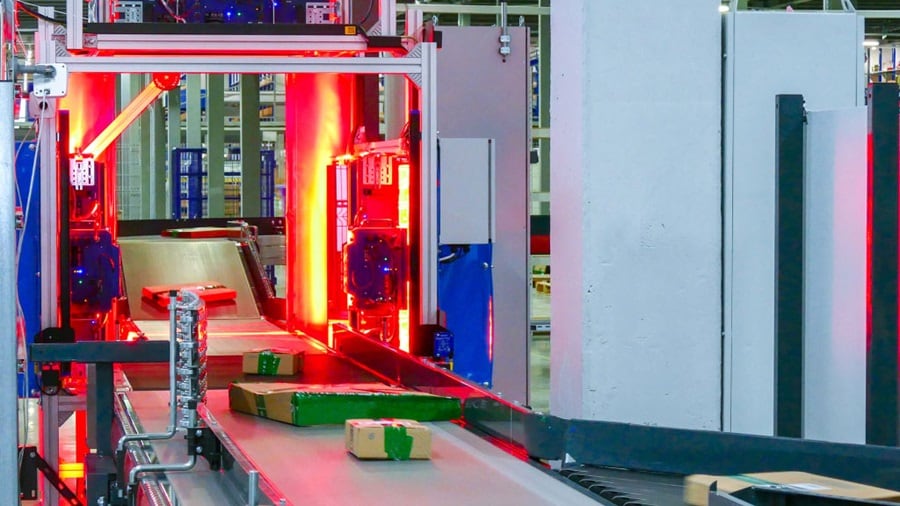
Milestones and achievements
On February 29, 2024, we inaugurated the RFID scanning system in Karachi, Pakistan. Our journey began in 2020 with manual scanning of 150-300 cartons per week. By early 2022, we implemented a gantry system, increasing capacity to 300-1,000 cartons per week. By the end of 2022, we automated the process and developed an app, boosting weekly scanning to 3,500 cartons. In 2023, we installed a conveyor Belt setup, further increasing the rate to 7,000-9,000 cartons per week. As of 2024, all five setups are operational, with an anticipated average scanning rate of 18,000 cartons per week. We are now working towards 100% cargo scanning.
Improved efficiency through automation and insight
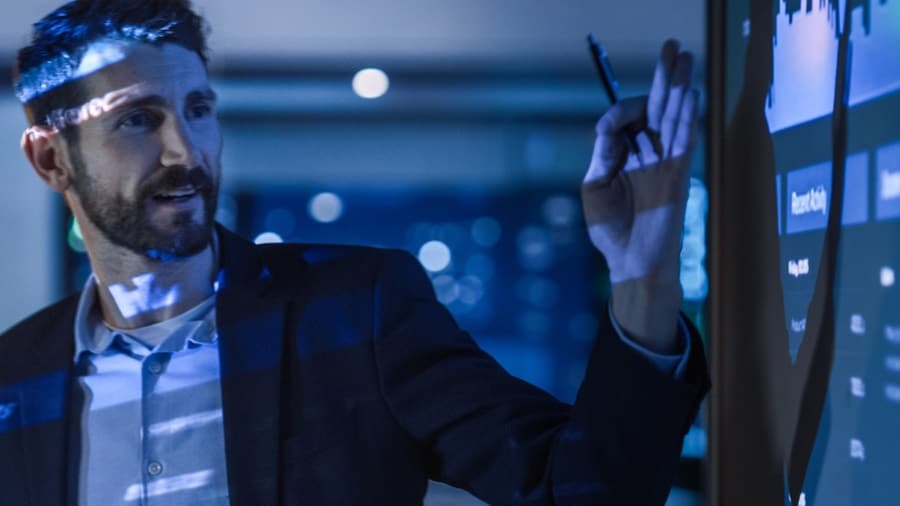
Logistics that scale with your business
This transformative journey has been driven by innovation, dedication, and a commitment to efficiency. Our team’s relentless efforts have resulted in a seamless and advanced RFID infrastructure, setting new benchmarks in scanning capabilities. As we enter this new chapter, we are excited about the possibilities this state-of-the-art setup brings to our operations. It’s not just about technology; it’s about enhancing accuracy, speed, and overall operational excellence.
The customer has since implemented RFID scanning at the origin, creating an annual value of $1 million. They are now looking to expand this solution to all major origins, including Egypt and Turkey, although there is no strict timeline for this expansion yet. They will require suppliers to install RFID systems in their facilities to scan and pack products, enhancing upstream visibility across the entire network from suppliers to downstream destinations. Numerous additional projects are being explored, such as using RFID to optimise their payment process, with more benefits expected to emerge.
无论您需要什么,我们都可以随时为您提供帮助
提交此表,即表示我同意通过电子邮件接收 A. P. 穆勒-马士基集团及其关联公司接收物流相关新闻和营销信息更新。我了解我可以随时通过点击退订链接,取消接收此类马士基推送信息。如需查看我们会如何处理您的个人信息,请查阅隐私公告。