The changes in consumer behaviour over the last few years have created huge fluctuations in supply and demand. The buying frenzy of the pandemic years created supply shortages across every sector. In response, many businesses increased production. But the economic slowdown of the last 1-2 years meant a decrease in consumer demand, leaving businesses with excess inventory at every point in their supply chain.
Those quick pace changes have made it more critical than ever for businesses to have visibility into their fulfilment operations. They need to know where they have inventory and how it can be moved in order to adapt to changes in the supply chain.
Historically, ad hoc systems running across multiple supply chain partners have increased complexity and costs in fulfilment. To provide a higher level of operational excellence and reliability, the industry must invest in more optimised fulfilment technology.
What is fulfilment technology?
Fulfilment technology is a broad category—it can be any combination of software, hardware and other technologies used to manage the process of order fulfilment. Simply put, it’s the technology ecosystem that gets your orders from the internet to your home.
Arguably, the biggest player in that ecosystem is the warehouse management system (WMS). A WMS serves as a central platform for all the activities within a warehouse: inventory management, order processing, picking and packing, shipping and receiving.
The average North American warehouse is about 2,300 square metres (about 25,000 square feet) -- meaning that a system that maximises space utilisation, inventory accuracy, enhances productivity and reduces errors is key to giving customers visibility into their inventory and improving efficiency in their supply chain.
How we’re driving operational excellence with a standardised WMS
As our fulfilment footprint has grown to over 660 facilities in 66 countries with an 11 million square metre footprint, we found ourselves with different warehouse management systems for different markets, geographies, etc. These different systems made it challenging for us to scale both the experience we offer customers and the experience our operators have using the systems.
To improve operational efficiency, visibility for our customers and create a better experience for our employees, we’re now rolling out the One Maersk WMS. The new WMS is built on the LF Logistics WMS, which has been developed over 20 years based on deep customer input. We’re further building on that system by creating a consistent user interface (UI).
This single UI allows us to scale our WMS across sites, regions, cultures and languages. It means that across all 660 fulfilment centres, we use one piece of software with one user interface. The new UI uses universal design principles so it’s intuitive to use and easy to onboard new operators. It also allows operators to switch between fulfilment facilities without a steep learning curve. Ultimately, that means we can streamline processes, minimise waste and optimise our operations.
What improved operational excellency means for our customers
Our goal is to provide the very best fulfilment services for our customers. By improving overall operational efficiency, we reduce lead times for our customers, improve shipment visibility and improve cost efficiency.
- Reduced lead times and improved order fulfilment accuracy. A single WMS allows us to streamline processes and optimise workflows, so orders are processed quickly and accurately. Since this system will be rolled out across all our fulfilment centres, we can achieve a higher rate of order fulfilment accuracy and reduced lead times regardless of where a customer’s orders are fulfilled.
- Greater visibility. By using a single WMS across our facilities, we’re standardising the data we collect and, therefore, the visibility we offer customers. Our WMS captures data for order fulfilment and stock movement through barcode scanning, mobile app data collection, automation and other technologies, ensuring data is up to date with each action, so customers can make data-informed decisions in real time.
- Scale meets customisation. By implementing a single fulfilment solution, we’re able to cover both day-to-day operations and sudden-scale large volume events like ecommerce promotions. We’re also standardising the way we offer customisable and flexible solutions, offering standard integrations with hundreds of ERPs, marketplaces, couriers and material handling equipment.
- Cost efficiency. The less waste we have throughout the supply chain, the more cost efficient it is for both us and our customers. Take, for example, variable fulfilment rates. The cost of fulfilment goes up when trade volumes are high. But by improving our operational excellence, our customers benefit from more consistent rates due to improved productivity and efficiency.
Four predictions for the future of fulfilment tech
While we’re making great strides in our operational efficiency by using a single, standardised WMS, there are many more gains to be made in fulfilment technology. We have four key predictions for how fulfilment tech will evolve in the near future.
1. The operator experience and customer satisfaction will be more closely linked
Recognising the crucial link between employee experience and customer experience, the future of fulfilment tech will prioritise more intuitive interfaces that give operators a better user experience. By leveraging better design, automation, AI-powered suggestions and advanced training tools, companies can empower their workforce, leading to higher efficiency and productivity and improved customer outcomes. Investing in the employee experience and enabling seamless collaboration will be pivotal in achieving exceptional service quality.
2. Fulfilment providers will strive for an ultra-reliable, Amazon Prime-like experience
As consumer expectations continue to evolve, businesses are racing to provide better and better experiences. As a result, they expect their fulfilment partners to keep up by providing an “Amazon Prime” like experience. Reliability will become the key deliverable and fulfilment providers will have to ensure orders are processed accurately, shipped promptly and delivered on the dot. To achieve this high level of dependability, fulfilment providers of all kinds will have to leverage advanced technologies such as real-time inventory tracking, optimised routing and predictive analytics.
3. More universal design systems will lead to more fluid job roles
Universal design principles are now de facto for consumer-facing platforms, but often B2B enterprise software doesn’t implement user-centric design (think of how easy it is to use Netflix or Amazon vs. how easy it is to use expense management or HR system at work). The future of fulfilment tech will bring the implementation of more usable, universal design principles, which will enable workers to transition seamlessly between different types of jobs within the fulfilment process. This flexibility not only enhances operational efficiency but also empowers workers to become versatile contributors, ultimately leading to smoother operations and improved productivity.
4. Beyond visibility: technology-driven recommendations and actions
While visibility remains crucial for customers, the future of fulfilment tech will go beyond simple monitoring and tracking. The focus will shift towards advanced technologies that provide actionable insights and intelligent recommendations. By harnessing the power of artificial intelligence, machine learning and data analytics, fulfilment systems will be able to proactively identify bottlenecks, predict demand fluctuations and suggest ways customers can optimise their fulfilment strategies. This proactive approach empowers businesses to make data-driven decisions, automate routine tasks and continuously improve operational efficiency.
Author:
Scott Horn is the SVP of Fulfilled by Maersk Platforms, responsible for the technology ecosystem behind all of Maersk’s fulfilment activities. Scott is a senior software engineering leader with over 20 years of experience designing and delivering large scale business transformations, building solutions that drive results and creating high performing teams.
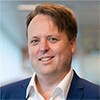
无论您需要什么,我们都可以随时为您提供帮助
提交此表,即表示我同意通过电子邮件接收 A. P. 穆勒-马士基集团及其关联公司接收物流相关新闻和营销信息更新。我了解我可以随时通过点击退订链接,取消接收此类马士基推送信息。如需查看我们会如何处理您的个人信息,请查阅隐私公告。