The protein industry is changing. The Organisation for Economic Co-operation and Development (OECD) has noted a stabilisation in meat consumption and forecasts anticipate a reduction. Despite this, protein producers have seen many years of strong growth in retail flows. So while the sector’s future is bright, it still faces challenges from outside the industry: geopolitical events that cause unexpected and wide-reaching disruption; growing focus on environmental considerations and increasing legislation; extreme weather events; influenza outbreaks, and national crises.
All this means that ’just-in-time‘ trade flows are vulnerable to a domino effect of delays. It’s clear that modern and efficient logistics, combined with a more resilient supply chain and innovative solutions for minimising disruption are essential to protecting margins.
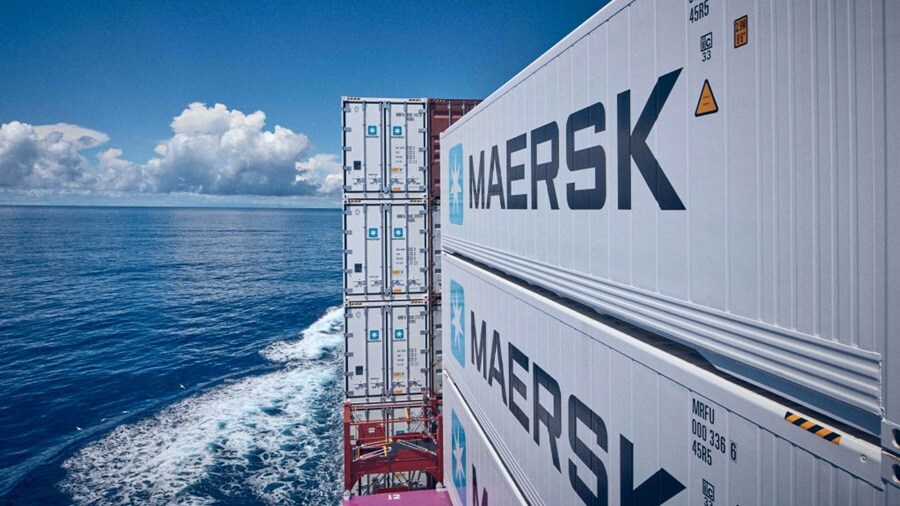
Addressing the issue of delays
When ‘watershed moment’ disruptions occur – like those caused by the Covid-19 pandemic, the Suez Canal block, or the Panama Canal drought – one challenge that suppliers are confronted with is the increase in transit time.
Prior to the Red Sea disruption, the average ocean transit time from Brazil to Asia was around 50-55 days. With the need to take alternate routes, this has now extended up to 70 days.
Though frozen produce doesn’t suffer the same time constraints as fruit and vegetables, predictable and reliable arrival dates are still critical for cash flow.
As a global logistics partner, Maersk can rapidly respond to these unprecedented, wide-scale disruptions, and help you to find solutions to increase the predictability of your supply chain.
With Captain Peter, our unique virtual reefer cargo assistant and remote monitoring tool, suppliers can track the precise location of containers from delivery to destination. In the event of unforeseen circumstances, it’s far easier to pivot strategies, redirect goods or reduce bottlenecks when you know exactly where your produce is and when it’s due to arrive – increasing not only the predictability of your supply chain, but the certainty of cash flow.
In cases where the original transit time is changed, Captain Peter’s remote monitoring of temperature fluctuations is critical to avoid the possibility of product waste due to warm-up.
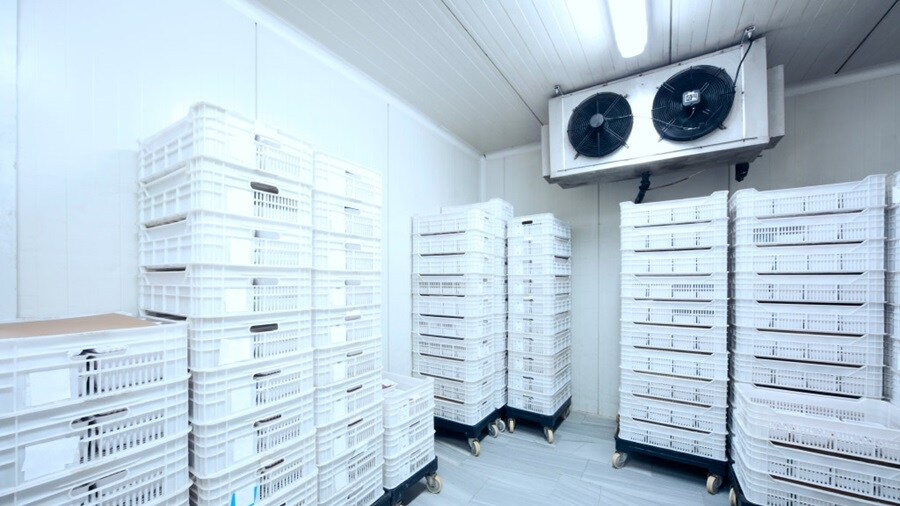
Using past lessons to plan for the future
During the Covid-19 pandemic, increased inspection times resulted in a hold-up in deliveries and wide-reaching disruption. Ports reached full capacity, meaning frozen produce could be wasted if it failed to reach a cold store facility in time.
Maersk devised a temporary floating storage space which could safely hold produce for up to 4 weeks, preventing warm-up and waste.
These ocean vessels had the necessary power to keep the containers at the correct frozen temperature for the entire duration, maintaining safety standards. 10% of our business is reefer, twice as much as the wider industry, giving us the scale and knowledge to find solutions to cold storage challenges.
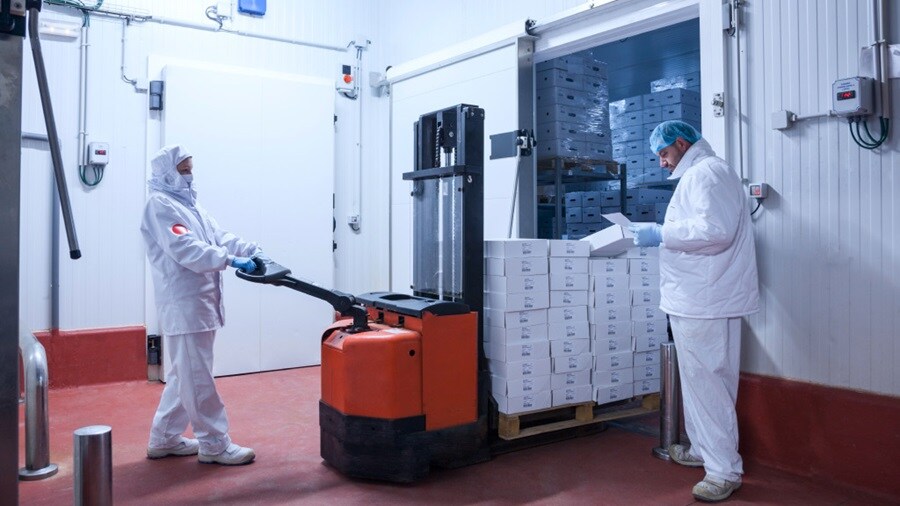
Effective anticipation through cold storage
While navigating past and present complications, ones that may arise in the future have to be considered as well. Avian influenza is a very real threat to the poultry supply chain. Outbreaks are currently impacting Europe and the US.
But a severe outbreak in Brazil, one of the leading producers and the source of around 45% of Maersk poultry shipments, could grind supply to a halt.
To prevent an avian influenza outbreak, or other disruptions in the country of production or en-route, from impacting your supply chain, you could re-examine your storage strategy. Producers often store goods for their domestic market near the point of consumption. But the same can’t be said for international cargo: many suppliers choose to store it in its country of origin. Doing this means your goods are vulnerable to incidents outside of your control that may occur between the point of manufacture and destination.
But if you store protein near the point of consumption internationally, you avoid these incidents ruining produce or delaying transit times, while increasing your speed to market. After all, in the event supply is massively disrupted, available produce becomes increasingly desirable!
Maersk is supporting these shifts in warehousing strategies with the development of cold stores. The majority of new or upcoming cold stores – such as our latest facility in the Maasvlakte II area of the Port of Rotterdam – are located close to ports or within port areas. This means fast and affordable shunting from port to store, but also links to nearby road, rail or barge networks that allow for quick transportation when it’s time to move the goods. All of this means your produce can be held as close to the point of consumption as possible.
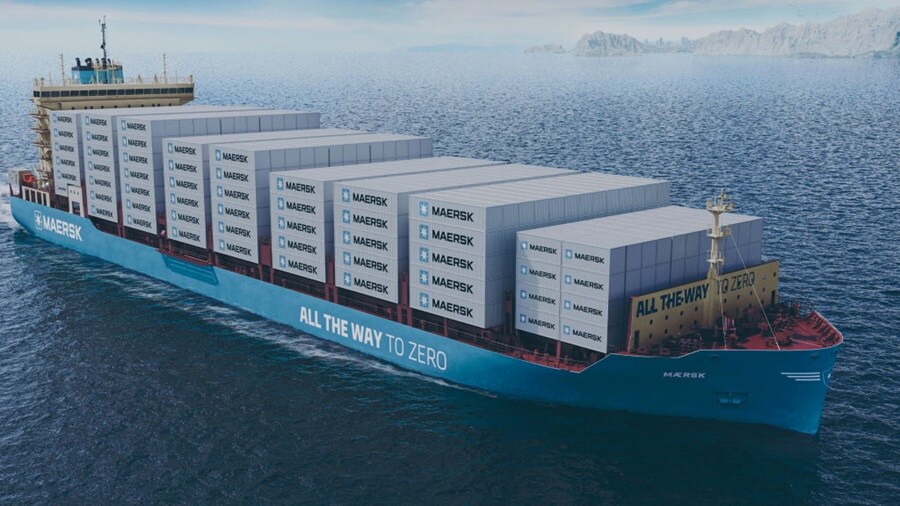
Shifting industry priorities
The ever-changing expectations of consumers mean that sustainability is a consideration for every industry, particularly protein. So much so, that many beef producers are now looking at genetic changes that can reduce the amount of CO2 emissions created by the produce.
If you aren’t in a position to dabble with genetics, it’s perhaps easier to look for suppliers that can comply with regulations and decarbonise your supply chain on your behalf.
In line with our net-zero greenhouse gas emissions target for 2040, Maersk has deployed the world’s first methanol-powered ocean vessels – a low-emission alternative to traditional fuels – with a total of 25 vessels on order. Each has a capacity of 16,000 containers, contributing to the decarbonisation of our customers’ supply chains.
We’re also considering customer emissions during the cold storage process when developing our new facilities. The Maasvlakte II cold store is being built with sustainability in mind. Designed to meet the ‘Excellent’ level of the BREEAM framework, the facility will have solar panels installed alongside water and heat recycling facilities. Proximity to nearby rail allows for the greater utilisation of this mode of transport, saving 75% emissions compared to trucks. And the use of electronic trucks from APM to cold stores and on-terminal locations also reduces transport emissions.
Across the globe, the consumption of protein remains high, but the industry can be a precarious one and “just-in-time” logistics leaves producers open to vulnerability. By partnering with a supplier with global reach and local market knowledge, you’ll be supported in responding to disruption and building resilience – minimising risk and maximising opportunity.
未来,您想随时了解必读行业趋势吗?
您已经完成了,欢迎“登船”!
出错了
未来,您想随时了解必读行业趋势吗?
使用此表格注册,即可直接在您的邮箱中接收我们的洞察见解,进入一个真正的综合物流世界。简单操作,即从我们为您量身定做的精选文章中获得启发,了解相关行业洞察信息。您可以随时取消订阅。
提交此表,即表示我同意通过电子邮件接收 A. P. 穆勒-马士基集团及其关联公司接收物流相关新闻和营销信息更新。我了解我可以随时通过点击退订链接,取消接收此类马士基推送信息。如需查看我们会如何处理您的个人信息,请查阅隐私公告。