When thinking about the current state of refrigerated logistics, two words come to mind immediately: challenges and innovation. Such different words, but intrinsically connected as one is the main cause for the other to come to life.
If you are shipping any cargo today, particularly if your products are perishable, you are certainly familiar with challenges. A global pandemic, delays, congestions, political instability, shortages, and several other issues are plaguing the world of container logistics and weakening the links of global cold chains.
Supply chain challenges are sparking fascinating innovation efforts, among both established players in the market for perishable goods as well as small start-ups, in areas ranging from pure data aggregation to new methods for extending shelf-life. There are huge opportunities to revolutionize and digitize the container logistics industry that is unfortunately still depending on unique paper copies for certain transport documents.
But what is currently at the top of the wish list for cold chain customers?
Levels of visibility
Visibility is becoming a buzzword within logistics. Typically, cold chain customers are looking for a level of visibility and control that can answer three simple questions:
1. When will my container arrive?
Customers want to know the exact time their refrigerated container is ready for pick-up from the terminal or when the trailer truck will arrive with their goods at the final destination. To meet this need, we are currently seeing an increased use of GPS trackers mounted on containers and GPS signals coming from the truck driver’s smartphone. Machine learning is also being applied to achieve more accurate arrival estimations taking both historic transport times and weather forecasts into account.
2. Will my cargo arrive in the expected condition?
Given the pandemic, customers are no longer able to travel as easily to destinations to check the quality of their cargo upon arrival. Now they need to rely more heavily on data points collected during the journey, and here temperature is the most important parameter to look at.
More container carriers are investing in infrastructure which enables a remote data flow from the container, and several customers are even applying temperature loggers themselves on a few pallets inside the container. Despite this, we are still in the early days of having a fully connected cold supply chain:
- The container temperature does not tell the full story of cargo which might also have travelled through packhouses and cold store facilities on both import and export side;
- Transmitting temperature loggers have so far been too costly to apply on every single pallet or box of a shipment;
- Combining data from different sources into a single overview is a challenge, unless you have one party handling the entire cold chain;
There is ongoing work on quality prediction models which can estimate the remaining shelf-life of certain perishable commodities based on parameters measured during the journey, but these models will in future be heavily dependent on data input from across the entire supply chain. New technology, such as smart- labels and sticker sensors, will soon come to a more realistic cost level and thereby enable reliable shelf-life predictions.
3. Has my container been opened by any unauthorized parties during the journey?
Container contamination, or even theft of cargo, are becoming a growing challenge for cold chain customers. Different compartments of a refrigerated container can be used by criminals to place illegal substances, unknown to the shipper or the receiver of the goods. Therefore, it is necessary for customers to know whether their container has been opened while in transit, especially during inland transportation or storage. Several types of door-opening and light detection sensors are becoming available in the market and we are seeing an increased interest from customs service and import/export authorities to collaborate with logistics providers on data sharing to achieve more intelligent inspection routines, and therefore reduce unnecessary disruptions to customers’ supply chains.
Enabling mitigating actions
Overall, the logistics industry is undergoing transformation in terms of digitization and data offerings, with great momentum around new visibility related solutions and technology. Once the above mentioned three customer needs for visibility have reached a satisfactory level, then comes the next question to the logistics providers: which mitigating actions can I take here and now if things are not going according to plan?
Serving customers with data is crucial, but the real benefits will only be achieved if the information is up-to-date, and everyone can interpret the aggregated data in the same way to take the right strategic decisions on the basis of it. That will be the next big leap in terms of optimizing global supply chains for perishable cargo to ultimately avoid cargo damage, contamination, or loss.
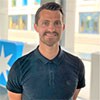
无论您需要什么,我们都可以随时为您提供帮助
提交此表,即表示我同意通过电子邮件接收 A. P. 穆勒-马士基集团及其关联公司接收物流相关新闻和营销信息更新。我了解我可以随时通过点击退订链接,取消接收此类马士基推送信息。如需查看我们会如何处理您的个人信息,请查阅隐私公告。