When it comes to warehousing, some logistics professionals argue that location is more important than cost. But are they right?
In this article, we’ll explore the cost and benefits of both factors and the role they can play in an end-to-end logistics strategy. Let’s dive in.
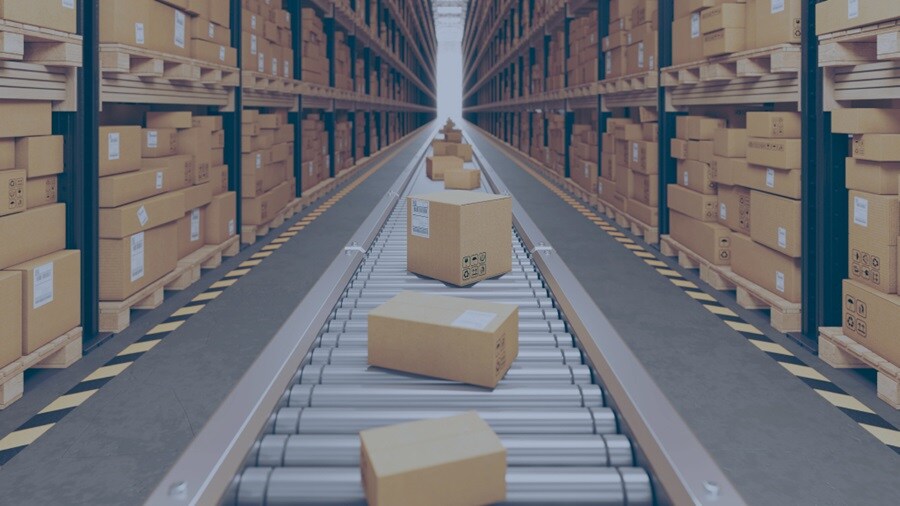
The case for proximity
Giving more weight to proximity when selecting warehouses can be highly advantageous. That’s because, with warehouses acting as the gateway to your markets, shortening the distance between business and consumer speeds up your delivery times. In fact, improving distribution methods like this can help online brands increase their competitive edge by more than 85%, according to ESW.
Not only will this help you gain a competitive advantage, but it’ll also help with your returns processes in your omnichannel strategy.
Supply chains flow in both directions, and a streamlined returns process means customers won’t have to wait a long time to receive a replacement.
Furthermore, in some instances, getting closer to key markets can also help reduce transport-related greenhouse gas (GHG) emissions, with the last mile being a prime example. At present, last-mile delivery accounts for 25-30% of emissions in towns and cities globally. It’s obvious, therefore, that action must be taken to lower this figure. Now here’s where warehousing can make a difference. Research from Accenture shows that positioning warehouse facilities nearer urban areas could reduce vehicle-related emissions by 16%-25% by 2025. That represents a potentially significant GHG emissions reduction.
However, it’s imperative to note that distance is just one of many factors used to calculate emissions. While reducing distances can have a large impact on reducing GHG emissions, optimisation of emissions impact by distance requires a detailed analysis and consideration of all factors, including the drivetrain, the type of energy used, the transport mode, the weight and the vehicle utilisation. Any decision taken to decarbonise your supply chain must consider all these factors.
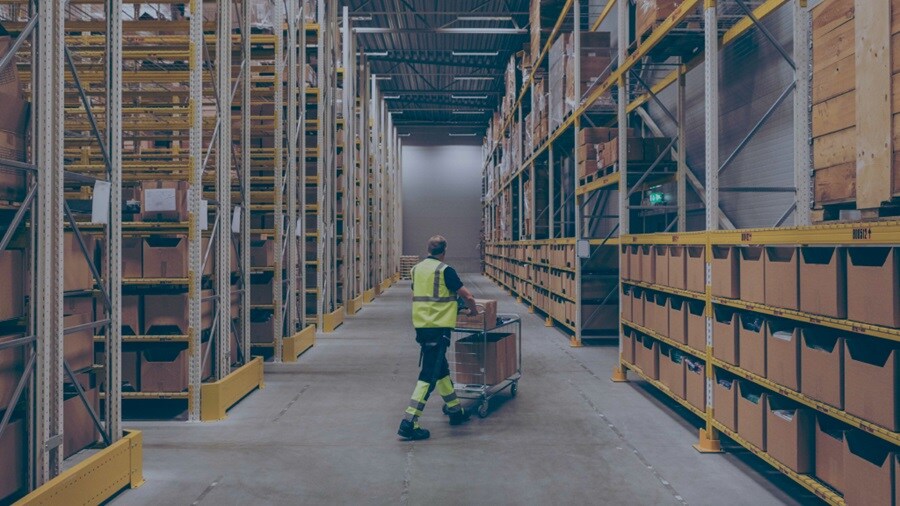
The case for cost
On the other hand, over the past few years warehousing demand has risen dramatically. According to data provided by Jones Land LaSalle (JLL), the total demand for warehouse and industrial space in European markets in 2021 increased 35% year-to-year and has stayed at that level since. Naturally, this is affecting price, with warehousing rent expected to increase by more than 10% in 2023, according to CBRE.
High demand for warehouse space and increasing rental costs gives retailers a problem.
They need to expand their warehousing footprint at a sustainable cost otherwise the whole exercise will be futile. So, to protect their bottom line and create cost efficiencies in the supply chain, is a better strategy to simply search for the cheapest available warehousing space?
Potentially, but not certainly. Increased rental costs need to be viewed in the wider context of economic downturn, where costs are also increasing for transport, energy and labour. Any cost savings achieved by choosing a warehouse with cheaper rent could potentially be negated by increased transport costs. Nevertheless, in the current financial climate, it’s hard to overlook the business case of a more stable balance sheet.
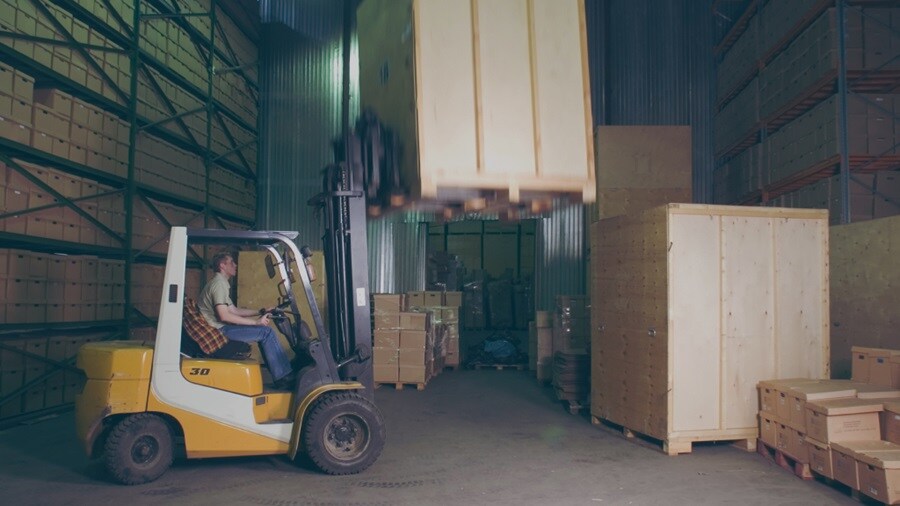
Striking the balance
Let’s be clear: retailers are businesses and that means overall operational costs and the bottom line will always come first. While proximity is an increasingly important factor and can be a major advantage for certain logistics strategies, it’s not the ‘raison d’être’.
But that doesn’t mean a balance can’t be struck between the two. Applying a hub-and-spoke distribution model, for example, is one way to strike that balance — you can speed up delivery by managing your high-selling SKUs in satellite facilities close to market, while lowering costs on your slower-moving SKUs by keeping them in the central warehouse.
However, it’s not always easy to spot these opportunities. That’s where an integrated logistics provider like Maersk can help. With our network of assets across Europe and the globe, combined with our teams of on-the-ground experts to advise you on the right warehousing, fulfilment and transport options, we can help you strike the right balance for your supply chain. Because in warehousing and distribution, like in life, balance is everything.
To find out more about Maersk's warehousing and distribution capabilities, visit our European Warehouse and Distribution page or for more information on warehousing strategy, download our latest eBook on efficient warehousing.
无论您需要什么,我们都可以随时为您提供帮助
提交此表,即表示我同意通过电子邮件接收 A. P. 穆勒-马士基集团及其关联公司接收物流相关新闻和营销信息更新。我了解我可以随时通过点击退订链接,取消接收此类马士基推送信息。如需查看我们会如何处理您的个人信息,请查阅隐私公告。